Identifying Deviations Earlier with Supplier Quality Management
With most issues, the earlier they are identified, the less negative impact they have in the long run. The same is true for quality management. For instance, if a deviation in a supplier production process slips by unidentified and unresolved, the further along the value chain that deviation makes it toward the customer, the greater its negative impact to profitability, reputation, and business performance in general.
The LNS Research 2012-2013 Quality Management Survey asked over 500 executives and decision makers in a wide range of batch, discrete, and life sciences manufacturing companies detailed questions about processes and technologies within their quality organizations. An important finding of this survey is the effectiveness of supplier quality management (SQM) in identifying quality issues early in the value chain.
SQM is a set of tools that enables communication and collaboration with suppliers and facilitates access to important real-time data. This added visibility has considerable benefits to manufacturing and quality key performance indicators (KPIs).
Supplier Quality Management Tools
Among the portfolio of SQM tools, there are three that stand out as instrumental in catching and resolving quality issues before they are even received at the shop floor: scorecards, portals, and statistical process control (SPC).
Scorecards: As a risk management tool, supplier scorecards enable organizations to quantify and prioritize risk based on the criticality to operations. Essentially, a quality team may develop a scorecard or leverage a software solution to assign a numerical value to each supplier in their network. This value would account for past and present performance in the following areas:
- Percentage of defective products received
- Percentage of returned products
- Chargebacks for non-conformances
- Complete and on-time delivery
- Percentage of products out of compliance or quality standards
Based on the performance in standardized metrics like the ones above, companies may create a risk score from 0-100 or 1-5 to rate suppliers based on multiple dimensions like failure frequency, likelihood, and impact. It is also beneficial to have multiple employees rate suppliers through a standardized risk scorecard to eliminate biases and develop a more comprehensive analysis of supplier performance over time. In maintaining an up-to-date risk scorecard for each supplier, executives and plant managers can make data-backed decisions that benefit the aggregate risk portfolio.
Portals: Typically delivered over the Web, portals open up a two-way line of communication and collaboration, and enable the level of visibility needed to get the most from supplier relationships. As an interface that facilitates the flow of real-time information, supplier portals help to bridge many of the traditional gaps that came with leveraging the global supplier network. By using supplier portals, organizations can experience improvements in the following areas:
- Order cycle time
- New products introduction
- Inventory control
- Compliance and quality standards
- Communicating best practices or SOPs
- Delivery times
- Production status
Statistical Process Control: Often leveraging Web-based technology as well, SPC helps manufacturers monitor variations in supplier processes with statistical analysis tools. Many large organizations now require suppliers to provide SPC data during the production process. By bringing together SPC and SQM, companies can greatly improve the ability to identify and resolve quality issues as close to their source as possible.
Proving the Value of SQM with Benchmark Data
One of the questions in the LNS Quality Survey asked respondents about the impact of SPC on overall equipment effectiveness (OEE), which is an important metric that measures a manufacturing asset’s availability, efficiency, and quality. As can be seen in the chart below, respondents that had currently implemented SPC showed a higher median OEE (89%) than respondents that had no plans to implement (76%), or those that had planned but yet to implement SPC (85%).
In addition, the distribution of responses is tighter with respondents that had implemented SPC than with those that had not.
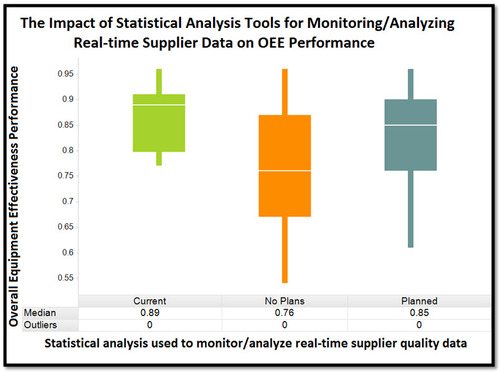
In defining a strategic objective, these and other SQM tools offer valuable methods for attaining quality goals and identifying issues before they migrate far into the value chain and cause increasing amounts of financial, operational, and reputational damage. Particularly for companies with a large number of suppliers, reviewing supplier risk scorecards and access to direct lines of communication through portals are vital components in effective supplier management, and important in achieving a model of operational excellence.