Buyer's Guide
Introduction to Air Compressors
Compressed air is used in almost every industry imaginable. It's so flexible and useful that it's often referred to as the fourth utility behind gas, water, and electricity.
Any business that makes anything has to "move" air and therefore, needs an air compressor. Automotive manufacturing, construction, mining, wood/metal/plastics manufacturing, and agriculture are obvious industries. Others like food and beverage, pharmaceutical, consumer goods, textiles, and electronics also utilize compressed air.
If you're in the market to purchase an air compressor, this buyer's guide can assist you in understanding the various models in order to choose the appropriate one for your company's needs.
There are three main classes of compressed air applications:
- Hand tools. On the smallest scale, compressed air can run huge range grinders, drills, nail guns and similar tools. Since they don't need internal motors, using air-power makes the tools lighter, cooler, more efficient and therefore eco-friendly.
- Manufacturing. Compressed air is ubiquitous as a source of power: to gently move products from one location to another, drive powerful punches or stampers, or power modern robotic tools.
- Specialty applications. Finally, some applications make more direct use of the air. Compressed air is essential in sandblasting, spray painting, inflating tires, filling scuba tanks, etc. It's commonly used for cleaning - from blowing metal shavings off a lathe to making sure semiconductors are dust-free.
To get started, familiarize yourself with the two main types. Luckily the choice at this stage is a pretty easy one: it depends on whether or not the application you're involved in requires continuous use. Find out how in the next section.
Basic Types of Air Compressors
For most industrial and manufacturing uses, there are two main types of air compressors to consider:
- Reciprocating compressors - In these machines, also known as piston-driven compressors, pistons compress the air in a cylinder and force it into a high-pressure storage tank. Piston-driven machines are the oldest and most affordable type of air compressor, and are most commonly found in portable applications or home workshops. Over one million piston air compressors are sold every year.
- Rotary screw air compressors - Instead of using pistons, rotary screw compressors use twin screws, like two over-sized drill bits next to each other, to force air up into higher pressures. They're designed to compress air more efficiently because they contain a cooling system. Until recently, rotary screw compressors were considerably more expensive than reciprocating models - now, prices are becoming more competitive. However, they're still costly and suited for heavy industry. Only about 25,000-30,000 are sold annually.
Both types are available in two-stage models that compress the air a second time to allow for increased pressure and air flow.
An important way to decide between these two is to consider whether your application is continuous use or intermittent. A nail gun, firing a burst of air every few seconds, is an intermittent tool, while a spray painter is used continuously. If your application calls for continuous use, you'll want a rotary compressor.
That's due to the rated "duty cycle:" the amount of time each hour that a compressor is able to work. A duty cycle of 75% means the air compressor needs to rest for 15 minutes out of every hour to cool down. Rotary compressors have a duty cycle of 100%, thanks to fewer moving parts and robust oil cooling systems. In contrast, reciprocating compressors are designed to run only part of the time.
Centrifugal compressors
A third major type is the centrifugal compressor. These high-end compressors are essentially turbine engines: they use rotating blades to create high pressure. They are almost exclusively used in power plants and huge industrial applications, simply because they begin to become economically competitive at a scale well beyond that of most users.
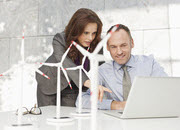
Common ratings
Knowing your requirements can help you decide which type of compressor is best for you. The largest two-stage reciprocating compressors max out at around 100 CFM (Cubic feet Per Minute), but in practice it's uncommon to see them over 50 CFM. Rotary compressors can reach 1500 CFM with a single stage and 2500 or more with two.
At the low end of the market, smaller air compressors - below 5 or HP - are almost exclusively piston-driven. And centrifugal compressors operate upwards of 1000 CFM and in a range of 400 to 8000 HP. At that size, centrifugal air compressors provide air at competitive costs.
Note that compressors are most commonly rated by horsepower, instead of CFM or PSI. A small home air compressor might produce 1.5 HP while large industrial compressors reach into the hundreds or even thousands of HP. The rule of thumb you can use to determine your approximate needs is that 1 HP should produce 4 to 5 CFM for rotary compressors, and 3 to 4 CFM for piston/reciprocating compressors.
Don't worry too much about horsepower when you're shopping: more efficient compressors can produce better CFM with less horsepower, and manufacturers have different methods of rating HP. Instead, stick with the CFM and PSI specifications.
With the type established, your next step is to focus on size. Here, the two terms you need to pay closest attention to are "pressure" and "air flow." Exactly how they come into play, how they’re measured, and how those measurements translate to operating power are all covered in the next section.
Sizing Your Air Compressor
You must be clear about your application in order to choose the right air compressor. Then follow these steps to determine the size.
1. Most tools and machines powered by compressed air will give you two important pieces of information:
- Air pressure (measured in PSI - pounds per square inch)
- Air flow (measured in CFM - cubic feet per minute)
Each piece of equipment will have requirements for both, "3 CFM at 90 PSI," for example. You can run multiple tools off the same compressor, too. So gather this information for every piece of equipment that will use the compressor.
If your equipment is old or lacking documentation you might not be able to get these exact figures. At least take note of the make and model information. Your compressed air seller will be able to make an educated guess based on the type of equipment.
2. Once you've gathered the requirements for each tool, add up the CFM figures for all the tools that will be used simultaneously - that's the minimum CFM to look for. The rule of thumb is to multiply that number by 1.5. This will give you a good margin of error in case some tools leak small amounts of air and keep you from overworking your compressor. Keep in mind the number of people using the tools simultaneously can affect the CFM. This likelihood is usually low, but it's a consideration, and the tank acts as a buffer.
3. Next, add up the number of users and multiply by .75 to calculate the PSI. You can also take the single highest PSI requirement from any tool, and round up slightly for a benchmark. If your tools require 90 PSI, buying an air compressor that provides the CFM you need at 100 PSI will make sure you always have enough pressure to run your equipment.
4. Once you have both these figures, choose an air compressor than can meet the CFM and PSI requirements at the same time. Some sellers will list CFM ratings at 45 PSI then tell you that the same compressor is capable of 90 PSI. It may be, but it might not be able to provide the same air flow at that pressure. Your reseller can help you figure this out. Don't hesitate to describe exactly what tools you'll be running and ask if the compressor is adequate for the job - then compare his answers to the written specs.
- NOTE: You may see some compressors rated in ACFM (actual cubic feet per minute) or ICFM (inlet cubic feet per minute). These represent essentially the same measurements as CFM.
Plan for expansion
When evaluating your compressed air needs, be sure to consider your plans for the future. Reciprocating/piston air compressors can last up to 30 years, providing it's properly applied and maintained well. Rotary air compressors are good for 10 to 15 years. They have more service points (belts, oil, filter, and separator.) Consider if you'll be adding more tools or more employees who'll be using the air simultaneously.
In addition, many businesses that introduce compressed air into their operations find additional applications that they hadn't anticipated, such as using it to clean up. While these applications may be less central to your production, they do increase demands on your compressor.
Air Quality and Other Considerations
It's important to note that a business has complete control over the production and quality of its compressed air. Depending on your needs, you may want to take steps to improve the overall quality of your air, especially if your compressor is going to power manufacturing automation equipment or other expensive machinery.
Because of the temperature changes involved its creation, compressed air can suffer from condensation that introduces moisture into the air delivery. In sensitive equipment such as CNC routers, any water is likely to cause problems and may void your warranties. To combat this, compressors can be equipped with driers that remove all traces of moisture.
Air from a compressor is also warmer than ambient air. It's simple physics: you put energy into air to compress it and that creates heat. Piston (reciprocating) compressors operate hotter. For every 20 degree increase, the humidity doubles. If your task requires lower air temperatures, you can add a cooler. For rotary screw air compressors, built-in coolers are standard. These coolers reduce the temperature within 10-20 degrees of ambient air.
Compressed air can also accumulate small particles of oil, dust, and other debris. Relatively inexpensive filters can remove these particles and protect your equipment.
A small investment in conditioning the air that comes from your compressor can protect a much larger investment: cool, dry, clean air can extend the life of your manufacturing equipment. A dryer acts like a refrigerator: it cools and condenses the air, then drains it away.
Oil-free air: rotary compressors
Because the oil required to lubricate compressor motors can sometimes leak into the air chamber, basic air-powered tools are generally tolerant of some oil in the compressed air. However, for applications such as working with food or semiconductors, as little as one part per billion of oil is unacceptable. In these cases, you'll need oil-free air.
Rotary air compressors have the ability to clean oil out of the air before it goes "downstream" and infects the air supply. These 50 HP+ machines are expensive to buy, power, and maintain; therefore they aren't as common.
Oil-less air: piston (reciprocating) air compressors
It's imperative to understand the difference between oil-free and oil-less. Oil-less compressors are not considered an add-on like dryers, coolers, or filters; they're a separate class of their own. Piston compressors consume the oil in a sealed off chamber, contrasted with rotaries that clean the oil. These are smaller (10 HP and below), specialized machines that are expensive for the common market. Dental, medical and laboratory industries require oil-less air compressors.
Heat and noise
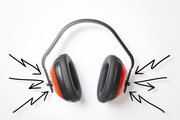
You should also consider the placement of your compressor. Compressors generate considerable amounts of heat. "Squeezing" air adds energy, which produces heat. Up to 96% of electricity that goes into an air compressor comes out as heat.
Compressors can also be extremely loud -over 100 decibels, in some cases. For comparison, sitting in the front row at a rock concert pounds out 120 db! These two factors lead many businesses to set up a "compressor room" where the heat can be vented and the noise contained, while air is distributed to where's it needed through long hoses or piping.
If you don't have the luxury of space, you may want to get an enclosure for the compressor to reduce noise levels. Remember that ventilation is essential; this helps the efficiency and longevity of your air compressor. Therefore, a closet is not ideal. Alternatively, you can choose a quieter type of compressor.
Rotary compressors are much quieter than reciprocating models. New rotary machines are not much louder than 65 db; the volume of typical conversation is 60 db.
Power
Compressors are usually powered by electricity. The smallest models run on standard 110v, single-phase power, but most commercial and industrial models need three-phase power. Often, you'll be able to specify the voltage (208v, 230v, 460v) the compressor should run on, so make sure you know what you have available.
If you're going to use your compressor outdoors, or move it around quite a bit, you'll want to choose a compressor with a gasoline or diesel engine. Portable compressors are used for various applications. For example, a gas powered compressor of 5-15 HP will be mounted on the back of a pick-up truck. A diesel engine of 20 HP+ may get transported on a trailer to a construction site. Internal combustion engines increase the noise and heat your compressor generates, but they are usually cheaper to operate than electric compressors.
Mobility
If your compressor is going to be mobile, you'll also want to pay more attention to the weight, wheels, and handles on the compressor. Towable larger engine-driven compressors for construction are often self-contained trailers, making it easy to move them from job site to job site. If you won't be moving it around but do have concerns about space, look for a compressor that's vertically oriented. It will leave you with more valuable floor space.
The above specialty considerations aside, air compressors have a definite impact in terms of cost.
Compressors and Energy Costs
Operating costs for an air compressor can be surprisingly steep. Estimates differ, but industry experts say that over a five or ten year span, you can expect the purchase and maintenance to comprise 15% each and the remaining 70% is the cost of energy to run your air compressor.
For example, start with a typical electricity cost of eight cents per kWh. At that rate, a 15 HP compressor running eight hours per day, six days a week, will use $2,000 to $3,000 in electricity annually. A 100 HP compressor in a two-shift operation can consume $35,000 in electricity in a year - much more than the initial cost of the compressor itself.
It's all relative to the size of the motor, the number of hours it's run, and the rate of electricity, which depends on your geographical area. Energy efficiency truly does matter.
The smart business shopper will recognize that saving 20% or 30% on the initial purchase cost is insignificant compared to the overall costs. Get the most efficient compressor you can, even if you pay a premium to get it by comparing the CAGI data sheetfor each model you're considering.
The Compressed Air and Gas Institute (CAGI) is a non-profit industry association that has developed standards for testing and reporting statistics on air compressors, including flow, pressure, horsepower - and expected energy consumption. The data sheets are similar to the yellow energy efficiency stickers you see on appliances: the net result is that you'll be comparing apples to apples.
Any seller should be able to provide the CAGI data sheet for the compressor you're considering. Also, some manufacturers make them available on their web sites. Be sure to include this step in your evaluation.
Now that you know the type and size you’re after and have prepared for the post-sale expenses, you’re just about ready to start talking to sellers. But before you do, take a quick look at the qualifying list below. We’ve compiled these considerations from a host of best practices to help you find the best combination of products and customer service.
Choosing an Air Compressor Seller
Air compressor sellers usually specialize in one brand, with manufacturers often requiring exclusivity from their sellers. The result is, you'll have to talk to a few different sellers to evaluate multiple brands.
On the other hand, because the sellers are forced to specialize, they develop a good understanding of the manufacturer's wide range of offerings and can usually do a very good job of supplying you with the right compressor for your needs.
In your research, be careful not to get overwhelmed with specifications and product claims. When buyers feel like they have too much information, they often wind up basing their purchase decision only on price, which is never a good idea. Take the time to talk to each seller and understand which compressor is right for you. You'll be far happier in the long-run owning the right compressor than you will be by saving a quick $500 up front.
Here are few characteristics to consider when comparing sellers:
- Longevity. How long as the seller been in business? A seller that's been selling air compressors for 15 or 20 years is obviously doing something right, and is more likely to be around in the future to support your purchase than one that is just entering the market.
- Dedication to compressors. Some sellers choose to offer a few air compressors simply as a convenience to their customers, even if the bulk of their business is in tools or supplies. If air compressors are the seller's main business, they're likely to have a better understanding of the systems.
- Strength of manufacturer. Most compressor manufacturers are well-established companies, but you should still check their commitment to the business. Some heavy equipment makers might make a small handful of compressors - it's advantageous to choose one that sells a full line of air compressors.
- Staffing. Does the seller have enough support and maintenance staff to protect and service your investment? Are they well-trained and experienced?
- Service rates. How much will you have to pay for repairs? Will they sell you a maintenance contract if you want one, or just sell you parts and let you do the work yourself if you prefer?
We also recommend that you ask potential sellers for references. Of course they'll supply you with references who are happy with them overall, but by asking the right questions, you can glean some good information:
- Ask about how often their compressor needs repairs and how quickly the seller takes care of them.
- Ask if they've purchased additional compressors, and if they bought them from the same source.
- And ask leading questions such as, "What could this seller stand to improve about their operation?"
We gathered the following pricing info on air compressors by averaging a wide range of national costs. Keep in mind: some aspects of your purchase may be negotiable. So make sure you have this data in your pocket when talking to a seller.
Air Compressor Pricing
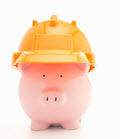
Since air compressors range from sub-1 HP home models to 10,000 hp industrial giants, there is an extremely wide range of prices. General pricing for basic types is fairly consistent.
At the very smallest end of the spectrum, the less than 2 HP market, you're probably better served going to Sears or Home Depot and buying one yourself, as opposed to going through a seller. You can get an adequate compressor for simple home use for under $500.
Most businesses will need something larger though. The low end of the heavy commercial/light industrial market is around 2-3 HP. That segment is dominated by reciprocating compressors that cost around $1,500 to $2,000, depending on the brand and size of tank you choose. At these low power levels, rotary compressors are more expensive. You'll probably pay $3,000 to $5,000 for a 5 HP rotary, the smallest in the light industrial market.
At around 10 HP, prices for reciprocating/piston run around $1,500 to $2,000 and rotary compressors cost in the neighborhood of $4000 to $8,000. A 25 HP is about as about as high as reciprocating compressors go, and that will range $7,000 to $9,000. A similarly rated rotary model will run you $9,000 to $12,000.
The 50 HP rotary models, one of the most popular sizes, go for $13,000 to $17,000. A 100 HP model will be $28,000 to $37,000, and a 200 HP unit will cost between $45,000 and $55,000.
See what other BuyerZone users paid for various types of compressors.Oil-free and oil-less compressors can drastically increase your costs. You can expect to pay almost triple what you would for a traditionally lubricated compressor of the same size.
Service agreements
Sellers will generally sell service contracts that cover parts and repairs along with the compressors. They're usually pretty flexible: if you have mechanics on staff and don't need that coverage, they'll be happy to simply sell you the parts you need. If the compressor is critical to your operations, you can sometimes pay extra for quicker service guarantees or around-the-clock coverage, but not all sellers will be able to offer this service.
Financing
There are a variety of financing options available, including 0% or $1 buyout leases, so inquire about these if the upfront cost is daunting. If you have a short-term need, monthly and weekly rentals are also available in many cases.
Packages
While the technology hasn't evolved greatly with air compressors, package purchasing has. Many resellers offer various packages beyond the solo compressor. For example you could buy a compressor on a tank, or a compressor plus tank, dryer, filter, and drain. You may want to explore package selections for long-term savings, convenience, and preparedness.
New vs. used air compressors
Most compressors are sold new, but there are small markets for both leasing and buying used equipment. Since compressors are often central to critical business processes, purchasing new equipment is usually your best bet. Also, air compressors are reliable and not subject to technological obsolescence. So owners tend to hang on to them for a long time, reducing the number available in the used market.
Buying new gets you the associated warranties and service contracts as well. Base manufacturers' warranties are 1 to 2 years "bumper to bumper," with additional years on major components.
Don't miss insider tips offered by some of BuyerZone's leading sellers. Popular for their ability to save you on your initial purchase, they can also help further extend the life of your air compressor.
Air compressor buying tips
Built to last. You can expect your compressor to last a long, long time. A rotary compressor has a life expectancy of 40,000 to 60,000 hours - that's 20 to 30 years at eight hours per day. You can expect at least 10 to 15 years from reciprocating compressors, and more if they're properly maintained. Consider all the costs beyond the purchase price: installation, maintenance, and energy.
Understand the differences between reciprocating (piston) and rotary: run time, energy use, air quality and how these apply to your industry.
Energy factors. If energy is important, consider a rotary and carefully review the CAGI data sheet to compare energy across models.
Down time. If your air compressor is vital to your business, don't risk the cost of lost production. Get an extra compressor as a backup instead of waiting for help.
Step up and down. Compressor manufacturers typically offer a wide range of models. If you find a brand and model you like that doesn't quite offer the power you need, there's typically another model that's one step up. Likewise, if you wind up over your budget, there's usually a slightly smaller unit you could consider, as well.